Katalysatoren
Exomission hat umfangreiche Erfahrung in der Auslegung, Trägerauswahl, Beschichtungsformulierung und den mechanischen und chemischen Haltbarkeiten verschiedenster Katalysatorsysteme. Wir bieten Ihnen sowohl Standardlösungen als auch speziell auf Ihren Anwendungsbereich angepasste Komponenten. Wir beliefern seit Jahren viele große und kleine Kunden. Wir beraten Sie gerne und freuen uns über Ihre Anfrage.
Der Oxidationskatalysator (OC)
Der OC ist für den Einsatz bei Motoren im Magerbetrieb konzipiert. Der Katalysator oxidiert Kohlenmonoxid (CO) und unverbrannte Kohlenwasserstoffe (HC) sehr effizient. Wirkungsgrade von 90% und mehr sind die Regel. Zu den Kohlenwasserstoffen zählen unter anderem auch nachfolgende Verbindungen:
- PAK - polyzyklische aromatische Kohlenwasserstoffe
- flüchtige organische Verbindungen
- nicht Methan-Kohlenwasserstoffe
- Aldehyde, beispielsweise Formaldehyd auch Methanal (CH2O) genannt
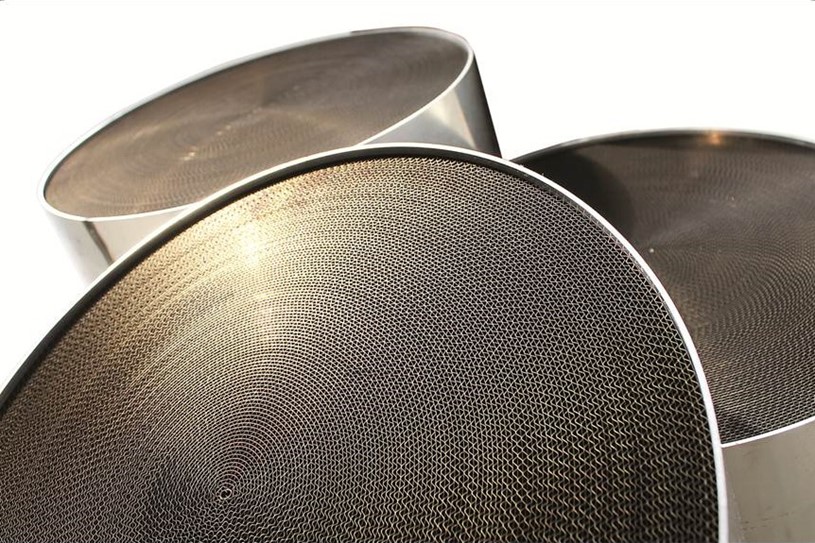
foto: ©fotolia.com
Der Biogaskatalysator (BOC)
Der BOC ist ein Oxidationskatalysator, der bei Verbrennungsmotoren (Mager- oder Zündstrahlverfahren) zum Einsatz kommt, welche mit Gasen biologischen Ursprungs betrieben werden. Dazu gehören Biogas, Grubengas, Klärgas und Deponiegas.
Der BOC oxidiert Kohlenmonoxid und Kohlenwasserstoffe. Zu den Kohlenwasserstoffen gehört auch Formaldehyd. Formaldehyd ist ein Zwischenprodukt bei der Verbrennung von Methan und fällt dadurch im Abgas von Biogasmotoren prinzipiell an. Die BOC von exomission sind mit einer speziellen katalytischen Beschichtung versehen, die eine erhöhte Beständigkeit gegen unerwünschte Schwefelverbindungen aufweist sowie die Oxidation von Schwefelverbindungen, wie erwünscht, generell verringert. Damit erhöht sich die Beständigkeit gegen Katalysatorvergiftung einerseits und verringert sich die Schwefelsäurebildung und damit die Korrosion der Abgaswärmetauscher andererseits.

Drei-Wege-Katalysatoren (TWC= Three Way Catalysts)
TWC sind für den Einsatz bei λ-geregelten Ottomotoren. Der Katalysator oxidiert Kohlenmonoxid (CO) und unverbrannte Kohlenwasserstoffe (HC). Gleichzeitig reduziert er Stickoxidverbindungen (NOx). Die gewünschten Reaktionen finden optimal beim Pendeln um λ = 1 statt. Hierbei spricht man von einem stöchiometrischen Kraftstoff-Luft-Gemisch. Im Falle von Benzin gilt ein Massenverhältnis Luft/Kraftstoff) von 14,7:1
Dieseloxidationskatalysatoren (DOC)
DOC oxidieren Kohlenmonoxid (CO) und unverbrannte Kohlenwasserstoffe (HC) bei Dieselmotoren.
Ein kleiner Teil der ausgestoßenen Partikel wird durch Oxidation der an den Rußpartikeln auskondensierten Kohlenwasserstoffen (HC) ebenfalls reduziert.
In Verbindung mit Partikelfiltern wird der DOC auch benötigt, um die ohnehin im Abgas vorhandenen Stickoxide (NOx) in Stickstoffdioxid (NO2) umzuwandeln; damit wird der Einsatz von passiv regenerierenden Partikelfiltern ermöglicht.
Wir können DOC mit Beschichtungen liefern die die NO2-Bildung behindern, als auch verbessern.